Design Pressure and maximum working temperatures shall be in accordance with project plans. Plate type heat exchanger uses metal plates to transfer heat between two fluids.
Plate Heat Exchangers Components Types Applications And Advantages
However plate heat exchangers which can operate at pressures up to 25 bar are available.
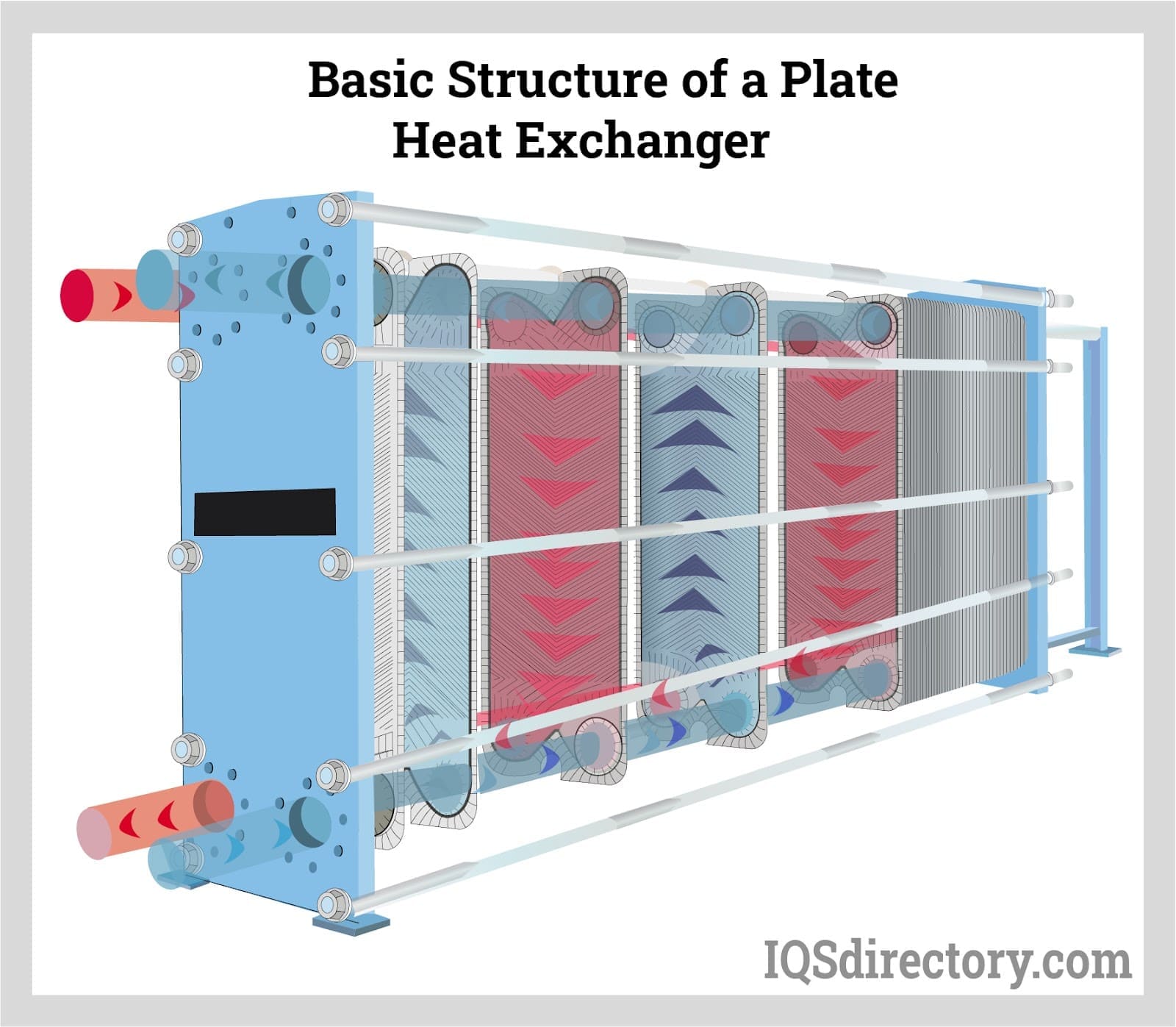
. UHX-191 b When the markings in accordance with UG-116 b 1 UG-116 c UG-116 e and UG-116 f are. Office of Scientific and Technical Information PO Box 62 Oak Ridge TN 37831 Telephone865-576-8401 Fax865-576-5728 E-mailreportsostigov. They were designed for engineers to do preliminary designs and.
H for plate heat exchanger is often in between 2 to 7 kWm 2 K -1. This abbreviation shall follow the appropriate letter designation and shall be separated by a hyphen. Welded semi-welded and brazed heat exchangers are used for heat exchange between high-pressure fluids or where a more compact product is required.
02 Rev 02 Feb 2020 These design guideline are believed to be as accurate as possible but are very general and not for specific design cases. CC 2766 is not covering fully brazed or fully welded plate packs. Hospitals office buildings more.
Plate Heat Exchangers for General Refinery Services Part II. Ad Get to know our product range for example our innovative enthalpy heat exchangers. Hospitals office buildings more.
Each plate in the plate pack is individually inserted into the frame in the correct order as per the final duty design. Thicker tubesheets or for high integrity service are made from forged discs. ASME units require ASME relief devices per UG-125 of ASME Code Section VIII Div.
Calculating the number of plates required. 2 T for tube side. θ η c 1 z 1 1 z 2 1 z 8 1 e λ 1 η c 2 z 1 2 z 2 2 z 8 2 e λ 2 η.
These fluids never encounter each other due to being separated by the heat exchanger. Where α heat transfer coefficient λ thermal conductivity. 3Once the plate pack is inserted the tie bars are put in place.
Compared to a plate-fin heat exchanger at matched flowrates pressure drop and heat exchanger effectiveness the manifold microchannel HEX had a 25 improvement in core heat transfer density kWkg implying that the heat exchanger provides more intense heat transfer per unit mass. The Plate Frame Heat Exchanger shall be designed and tested to the latest ASME Code Sect. There are four main types of phe.
12 rows Guide for the mechanical design materials selection fabrication inspection testing and preparation for shipment of plate-and-frame heat exchangers for use in petroleum industries applicable to gasketed semi-welded and welded plate-and frame heat exchangers. The asme code or en code we choose. TYPICAL PLATE HEAT EXCHANGER ASSEMBLY PROCEDURE The plate heat exchanger frame and connections are assembled and the plates start to be put in place.
Of Process Equipment Design PLATE HEAT EXCHANGER SELECTION SIZING AND TROUBLESHOOTING ENGINEERING DESIGN GUIDELINES Page 7 of 97 Rev. This was even taking into account the minimum wall thickness of 05 mm in the. Clad plate is commonly used where high alloy material is required for process reasons.
Different for each chamber the chambers shall be abbreviated as. For a perfect climate where humidity and purity count. Typically a plate heat exchanger will consist of several parallel plates positioned above each other thus creating a passage in which the fluid can flow between.
In 10 the design of a new plate heat exchanger and its cost were compared to heat exchangers available on the market. Plate Heat Exchanger Design. 23 STEP 3.
A plate heat exchanger is used to transfer heat energy from one fluid to another. In place of a pipe passing through a chamber there are instead two. The methodology employed for the design of a phe is the same as for the design of a tubular heat exchanger.
The Heat Exchange Design Handbook contains two chapters discussing these factors. Code dGermen Update READMEmd a41af30 on Oct 8 2021 6 commits READMEmd Plate_Heat_Exchanger_Design In the repository code report and data files can be found for plate heat exchanger design. 20 Mar 17 1214 I found the Code Case 2766 it does not require any design calculations or proof testing for establishing the MAWP for gasketed plate packs provided all 6 conditions of CC2766 are met.
In a plate heat exchanger the heat transfer can best be described by a Dittus-Boelter type equation. The production of heat exchangers the medium is a. The heat exchanger can be designed for heat recovery where plate heat exchanger efficiency can be up to 90 while using a tubular heat exchanger.
H overall heat exchange coefficient kWm 2 K-1 S area of the heat exchanger m 2 ΔT ml K The value of S can thus be calculated as a 1st approximation of the heat exchanger size. 64 design pressure operating a plate heat exchanger. The Plate Frame Heat Exchanger shall be designed and tested to the latest ASME Code Sect.
Reference is made to BP GS 126-5. MAWP of other pressure retaining parts will govern the design. By geometry and heat transfer analysis the total number of plates the actual with fouled surface and required heat duty are found as 105 plates 263 x 107 W and 232 x 107 W respectively.
1 S for shell side. 1 Preventing Excessive Pressure. This page will be updated as I have more time.
PSHE Construction The principle of a heat exchanger is to transfer heat from the primary to the secondary side through a heat-transfer plate that separates the flows. This part of 15547 gives requirements and recommendations for the mechanical design materials selection fabrication inspection testing and preparation for shipment of brazed aluminium plate -fin heat exchangers for use in. Tubesheets less than 100 mm thick are generally made from plate material.
The nominal thickness of gasketed plates before being pressed shall be sufficient to meet design conditions but shall not be less than 05 mm 002 inch. The plate heat exchanger PHE is a specialized design well suited to transferring heat between medium- and low-pressure fluids. The goal of the project is to understand the characteristics and design of a plate heat exchanger.
Reports are available to DOE employees DOE contractors Energy Technology Data Exchange representatives and International Nuclear Information System representatives from the following source. For a perfect climate where humidity and purity count. Vahterus heat exchangers are used for heating cooling condensing evaporating and the recovery of process heat.
A universally accepted code for shell and tube exchangers is TEMA 1988 which although designed to supplement ASME VIII can be used in conjunction. PFHEs are not recommended for design pressures above 30 bar abs 435 psia and design temperatures above 260C 500F. 1 Typical values of the constant and exponents are where d is the equivalent diameter defined in the case of the plate heat exchangers as approximately 2 the mean gap.
The normal maximum operating pressure for a plate heat exchanger is generally 16 bar for ASME-code units. Ad Get to know our product range for example our innovative enthalpy heat exchangers. Read the project report pdf for more information.
A Layout Of Chevron Type Pate Heat Exchanger Download Scientific Diagram
Plate Heat Exchanger China Manufacturer
Brazed Plate Heat Exchanger 40 Plates 5 X12 1 1 4 Mpt 530 000 Btu Heating Systems Heat Exchanger Domestic Hot Water
Maintaining A Plate Heat Exchanger 2002 03 01 Process Heating
The A One Pass And B Two Pass Internal Configurations Of The Brazed Download Scientific Diagram
Mechanical Information S Source Plate Heat Exchanger Parts Heat Exchanger Refrigeration And Air Conditioning Electrical Diagram
Basic Dimensions Of The Gasket Plate Heat Exchanger Download Scientific Diagram
0 comments
Post a Comment